सारांश
TCU तापमान नियंत्रण प्रणाली उच्च और निम्न तापमान क्षेत्रीय गर्मी या ठंड को नियंत्रित करने वाले सम्पूर्ण सुविधा उपकरण का समूह है जिसमें शामिल हैं उच्च कार्यक्षमता वाले ऊष्मा विनिमयक, परिपथन पंप, तापमान मापक, दबाव मीटर, विभिन्न सेंसर, पाइपलाइन, वैल्व और स्वचालित नियंत्रण। मानकीकृत मॉड्यूलों की डिज़ाइन अवधारणा पर निर्भर करते हुए, नेतृत्व के साथ प्रौद्योगिकी और समृद्ध व्यावहारिक अनुभव को मिलाकर, युआनहुऐ एक बड़ी समाकलित करता है उपयोगकर्ताओं के साइट पर सेन्ट्रीफ्यूगल पम्प, वैल्व का चयन और पाइप फ़्लेंज़ वेल्डिंग कार्य, बिजली के नियंत्रण की साइट स्थापना और समेकन कार्य को एक साथ करता है, और उपयोगकर्ताओं के लिए समग्र योजनाएं बनाता है ताकि उन्हें अधिक उपयुक्त सेट बनाया जा सके। उच्च और निम्न तापमान ऊष्मा विनिमय इकाइयों के साथ।
उत्कृष्ट प्रदर्शन। इसमें औद्योगिक नियंत्रण भी शामिल है, पूरी इकाई कारखाने से बाहर निकलने से पहले, कारखाने में परीक्षण स्टैंड पर परीक्षण चलाया जाता है और योग्य परीक्षण चलाया जाता है। उपयोगकर्ताओं को इकाई के इलेक्ट्रिकल कंट्रोल बॉक्स तक चार से पांच पाइपलाइन और एक बिजली की लाइन इंस्टॉल करनी होती है ताकि इकाई को डिबग करने और चलाने के लिए तैयार किया जा सके।
विशेषताएं
● उपयोगकर्ताओं को चौड़े तापमान की सीमा में बंद और पुनरावृत्त तापमान नियंत्रण प्राप्त करने के लिए सक्षम होने का समर्थन करता है, जिससे -20°C से 300°C (वैकल्पिक) तक तापमान नियंत्रण संभव होता है।
● पारंपरिक उपकरण सुविधाओं और जैकेट रखरखाव की आवश्यकता को खत्म करता है; छोटा द्रव आयतन नियंत्रण परिपथ की त्वरित प्रतिक्रिया को सुनिश्चित करता है और ऊष्मा प्रतिक्रिया देरी को न्यूनतम करता है।
● इंटरनल इलेक्ट्रिक हीटिंग हीट-कॉनडक्टिव ऑयल अपनी सिस्टम स्वचालित रूप से आवश्यकता के अनुसार सहायक हीटिंग सिस्टम को सक्रिय कर सकता है, भाप के उपयोग के दबाव को कम करता है। यह त्वरित संचालन के माध्यम से विभिन्न ऊष्मा मांगों को सटीक रूप से मिलाने में सक्षम है जिससे ऊर्जा-बचाव के उद्देश्य प्राप्त होते हैं।
● पूरे रासायनिक प्रतिक्रिया प्रक्रिया के तापमान को त्वरित गणनाओं के माध्यम से नियंत्रित करता है, पूरे रासायनिक प्रतिक्रिया प्रक्रिया के दौरान एक्सोथर्मिक और एंडोथर्मिक प्रतिक्रियाओं के लिए त्वरित प्रतिक्रिया नियंत्रण प्रदान करता है।
● मानकीकृत इंटरफ़ेस वास्तविक आवश्यकताओं के आधार पर गर्मी और ठंडी स्रोत ऊष्मा विनिमय मॉड्यूल्स जोड़ने के लिए रिजर्व किए जाते हैं।
● विकल्प रासायनिक प्रतिक्रिया प्रक्रिया के तापमान और एकल द्रव का तापमान को नियंत्रित करने के लिए उपलब्ध हैं। रासायनिक प्रतिक्रिया प्रक्रिया के तापमान और ऊष्मा-अनुकूल एकल-द्रव के तापमान के बीच का तापमान अंतर समायोजित और नियंत्रित है।
● एकाधिक कोइल्ड हीट एक्सचेंजर स्टेनलेस स्टील से बने हैं, जो संक्षारण प्रतिरोधी, उच्च-दबाव प्रतिरोधी और उच्च ऊष्मा विनिमय कفاءत वाले हैं।
● सूत्र प्रबंधन और उत्पादन क्रमवारी अभिलेखन के लिए पूरी तरह से बंद पाइपलाइन डिज़ाइन अपनाता है।
● प्रणाली प्रतिक्रिया तापमान को सัญญาณ स्रोत के रूप में उपयोग करती है; कंट्रोलर गणना करता है और विद्युत-संचालित वाल्व को कार्यान्वित निर्देश देता है, जिससे अभिक्रिया बर्तन के जैकेट में कम-तापमान द्रव का प्रवाह नियंत्रित होता है और कुशल नियंत्रण प्राप्त होता है।
● प्रत्येक तापमान नियंत्रण मॉड्यूल अभिक्रिया बर्तन के तापमान को नियंत्रित करने के लिए एक अलग PLC प्रणाली का उपयोग करता है। तापमान नियंत्रण मॉड्यूल विस्फोट-प्रतिरोधी क्षेत्रों में स्थापित होते हैं (विद्युत, उपकरण, आदि, विस्फोट-प्रतिरोधी आवश्यकताओं को पूरा करते हैं Ex dI IBT 4/Ex dI ICT 4)।
● कंट्रोलर एक अग्रिम अनुकूलन योग्य प्रोग्रामेबल कंट्रोलर का उपयोग करता है, जो अभिक्रिया बर्तन में पदार्थ के तापमान का सटीक नियंत्रण प्रदान करता है।
● प्रणाली नियंत्रण क्रम में अतिरिक्त या दोलन नहीं करती है, तापमान नियंत्रण की सटीकता ±0.5°C है।
विशिष्ट अनुप्रयोग
तापमान नियंत्रण इकाइयां (TCU) रसायन और फार्मासूटिकल उद्योगों में तापमान को सटीक रूप से नियंत्रित करने के लिए डिज़ाइन की गई विशेष उपकरण हैं। इन्हें प्रतिवर्ती तापमान नियंत्रण, लगातार गर्मी और ठंड, स्थिर तापमान, भापन, और क्रिस्टलीकरण प्रक्रियाओं के लिए उपयोग किया जाता है। ये विशेष रूप से अभिक्रिया के दौरान ऊष्मा उत्सर्जन या ऊष्मा अवशोषण वाली प्रक्रियाओं को नियंत्रित करने के लिए उपयुक्त हैं। विशेष रूप से सहजीकृत उपकरण की तापमान श्रेणी -120°C से +300°C तक पहुंच सकती है (साइट स्थिति पर निर्भर या कंप्रेसर और बिजली से गर्मी तापमान बढ़ाने और घटाने के लिए सहायक जोड़ने पर।)
इकाई के लिए तापमान श्रेणी: चयन के लिए एक विस्तृत तापमान श्रेणी -25°C से 135°C, -100 से 100°C, -20 से 200°C, RT से 300°C और अन्य तापमान अंतराल। दबाव श्रेणी: 0-1.0 MPa; उपयोग क्षेत्र: विभिन्न विस्फोट-प्रतिरोधी और विस्फोट-अप्रतिरोधी क्षेत्रों में उपयोग किया जा सकता है।
उत्पाद पैरामीटर
मॉडल |
YHO-30 |
YHO-60 |
YHO-90 |
YHO-120 |
YHO-180 |
YHO-250 |
YHO-300 |
YHO-350 |
तापमान श्रेणी ( ℃ )
|
’-20~135, ±1 ℃
|
पंप प्रवाह (m³⁄h) |
3.5 |
6 |
10 |
15 |
20 |
30 |
35 |
50 |
धुन गर्मी क्षमता (KW) |
30 |
60 |
90 |
120 |
180 |
250 |
300 |
350 |
शीतलन क्षमता (KW) |
25 |
45 |
65 |
100 |
150 |
210 |
260 |
300 |
ठंडे पानी का आयात और निर्यात |
DN25 |
DN32 |
DN40 |
DN40 |
DN50 |
डीएन65 |
डीएन65 |
DN80 |
उपकरण का आयात और निर्यात |
DN25 |
DN32 |
DN40 |
DN40 |
DN50 |
डीएन65 |
डीएन65 |
DN80 |
नियंत्रण प्रणाली |
पीएलसी नियंत्रक
|
पाइप सामग्री |
एसयूएस304 |
संपीड़ित वायु |
P≥0.5Mpa RT |
फ्रिज़न वॉटर |
P=0.2~0.3MPa T≤-25 ℃
|
विस्फोटायुग्मक आवश्यकताएं |
अ-विस्फोटायुग्मक/विस्फोटायुग्मक (वैकल्पिक) |
सुरक्षा संरक्षण |
स्व-विनिदेश, अधिक वोल्टेज, देरी, अधिक धारा, अधिक तापमान, कम तरल स्तर और अन्य सुरक्षा सुरक्षण कार्य |
डेटा आउटपुट |
यू डिस्क डेटा एक्सपोर्ट का समर्थन करता है और TXT फ़ॉर्मेट में तापमान डेटा एक्सपोर्ट कर सकता है |
शिष्टाचार |
MODBUS RTU प्रोटोकॉल RS485 इंटरफ़ेस (वैकल्पिक RS232/इथरनेट) |
नियंत्रण मोड |
सामग्री का तापमान और उपकरण का बाहरी तापमान स्वचालित रूप से चलाया जा सकता है |
संचालन पैनल |
7-इंच रंगीन छूने योग्य स्क्रीन (स्क्रीन आकार वैकल्पिक) |
खोल सामग्री |
कोल्ड रोल्ड प्लेट स्प्रे मॉल्डिंग/SUS304 (वैकल्पिक) |
पावर सप्लाई |
220/380V, 50/60Hz |
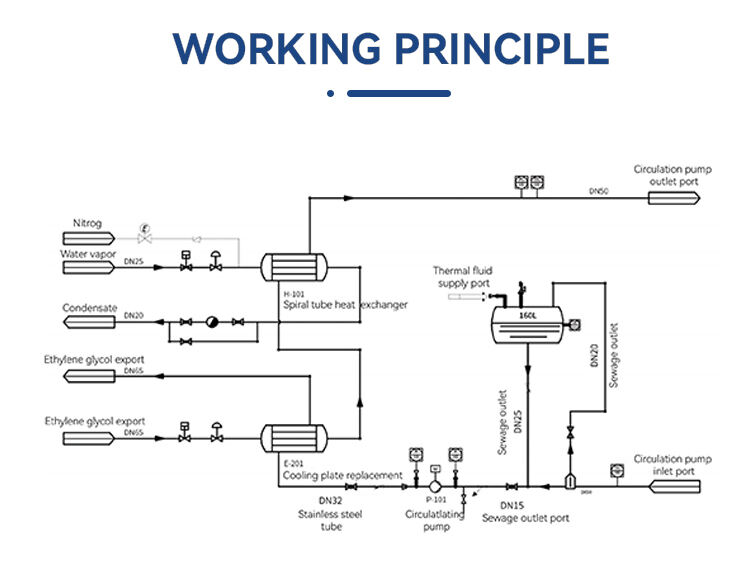